The main drivers of innovation in the automotive industry fall into three main categories: enhancing safety, protecting the environment, and improving convenience through interconnectivity. To achieve these goals, automakers, suppliers, governments, academia and even companies outside the traditional automotive industry (such as wireless chipmakers, mobile device manufacturers and wireless service providers) are all involved in developing advanced driver assistance systems (ADAS), connected vehicle technologies and, ultimately, self-driving cars.
ADAS and autonomous vehicles require high bandwidth and low latency networks to connect all sensors, cameras, diagnostic tools, communication systems, and central artificial intelligence.
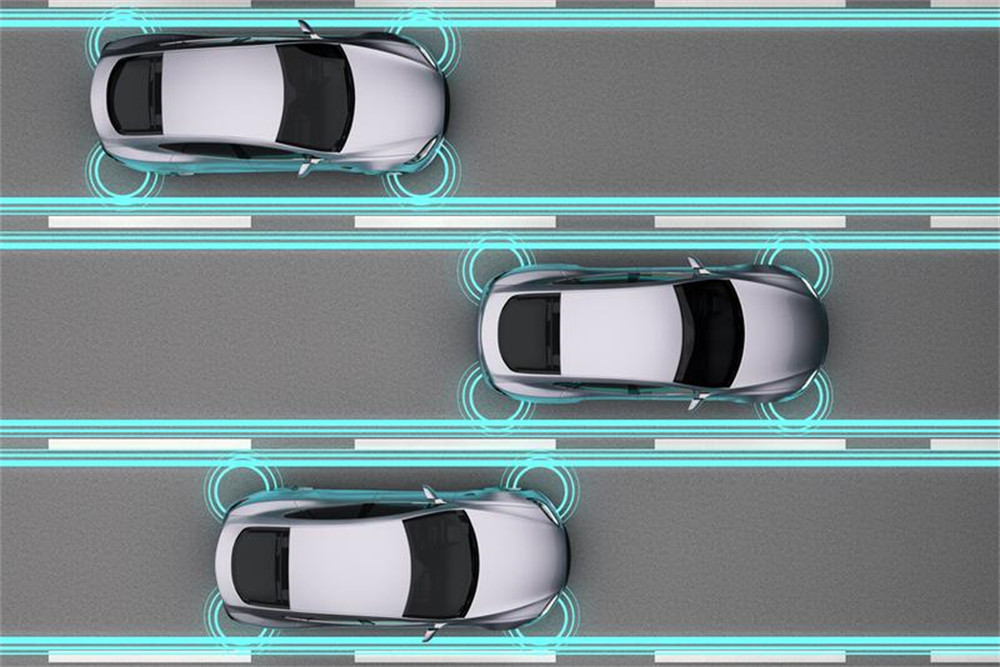
Automotive Ethernet is the emerging solution to these challenges. Just as WiFi is the cornerstone of dedicated short-range communications, Ethernet is a well-known, trusted and widely used solution in the traditional LAN space. Ethernet has many advantages, such as multipoint connectivity, wider bandwidth and low latency, that make it very attractive to automotive manufacturers. Still, when used in automobiles, traditional Ethernet is too noisy and susceptible to interference. To meet the specific needs of the automotive industry, IEEE has now developed new standards and protocols.
Capture and Process More Data Faster
The various technologies used in self-driving vehicles apply numerous new electronic components. The first category supports the fusion of sensors used in radio detection and ranging (RADAR), laser detection and ranging (LIDAR), and cameras. The second category includes vehicle-to-vehicle (V2V), vehicle-to-network (V2N), vehicle-to-infrastructure (V2I), vehicle-to-pedestrian (V2P), vehicle-to-utility (V2U), and vehicle-to-vehicle networking (V2X) wireless communications. A variety of adjacent components, such as high-definition (HD) maps using high-precision navigation systems, powerful signal processing, and artificial intelligence, are all required for autonomous driving.
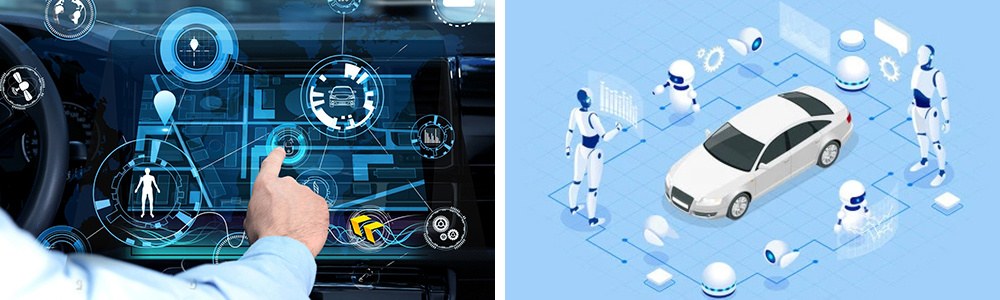
These technologies generate, send, receive, store, and process massive amounts of data. For example, a LIDAR module can provide highly accurate, high-resolution 3D and 360° imaging data around a vehicle. a LIDAR module may generate 70 Mbps of data traffic, a camera may generate 40 Mbps, a RADAR module may generate 100 Kbps, and a navigation system may generate 50 Kbps.
In addition, the higher the level of the autonomous driving system, the number of independent sensors grows tremendously, and the total amount of data generated as a result. For example, a Level 2 autonomous driving system can provide both longitudinal and lateral vehicle motion control, so the driver can let go and give his or her eyes a break. This system may require the use of five radar sensors and five cameras. A fully autonomous driving system (Levels 4 and 5) would require up to 20 radar sensors and six cameras, and would also use V2X communications.
We predict that a self-driving car will generate about 4 TB of data per day, and automotive Ethernet-based high-throughput, low-latency networks excel at transmitting, storing and sharing data over high-speed, reliable networks with very short latency.
What is Automotive Ethernet
Automotive Ethernet is a wired network for connecting electronic components in automobiles. It was originally designed to meet the automotive industry’s requirements for bandwidth, latency, synchronization, interference, security and network management. Originally conceived by Broadcom, the OPEN (One Pair Ethernet) consortium adopted the standard and assumed management responsibilities.
OPEN promotes Broadcom’s 100 Mbps BroadR-Reach as a multi-vendor licensing solution. 100 Mbps PHY implementation draws on the technology of 1 Gbps Ethernet, enabling 100 Mbps over a pair of cables. It enables 100 Mbps bi-directional transmission over a pair of cables. This technology uses a more advanced coding scheme that eliminates echoes and reduces the fundamental frequency (from 125 MHz) to 66 MHz, enabling Ethernet to meet automotive EMI specifications.The IEEE and OPEN Alliance have developed and maintain the physical layer standards for 100 Mbps and 1000 Mbps automotive Ethernet in the IEEE 802.3 and 802.1 groups.
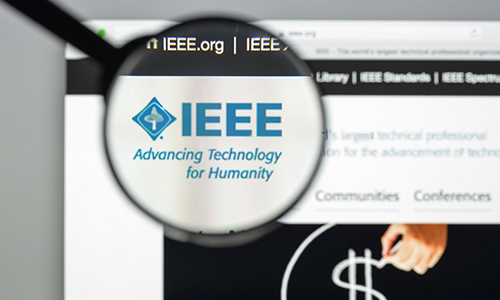
Why Automotive Ethernet
Automotive Ethernet offers significant advantages over traditional automotive serial buses for connectivity and communication in in-vehicle electronic systems, as well as for autonomous driving and ADAS systems. The complexity of automotive electronics architecture is increasing, with more sensors, controllers, and interfaces, demanding higher bandwidth, more computers, and communication links. Among automotive components, the wiring harnesses that connect these systems currently rank third in weight and cost.
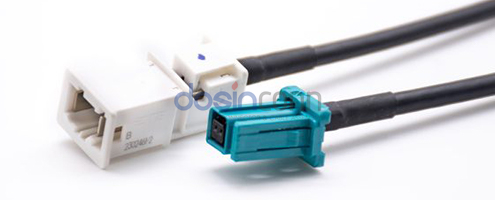
Automotive manufacturers currently employ various proprietary standards to enable communication capabilities, with most components relying on dedicated lines or cables. Automotive Ethernet, on the other hand, offers a unified standard that supports all communications. It utilizes a pair of cables to connect each electronic component to a central network switch. By utilizing unshielded twisted pair (UTP) cables and smaller, compact connectors, connection costs can be reduced by up to 80 percent, and cable weight can be reduced by up to 30 percent.
The Future of Driver Assistance Systems
Autonomous driving and ADAS will benefit society, but they will also create many new testing challenges for engineers. The current automotive demand for high data rates, bandwidth and data security continues to increase, while also requiring greater preparedness for future needs. To this end, Automotive Ethernet provides the necessary advanced features and overcomes the shortcomings of traditional automotive serial buses for the connectivity and communication of in-vehicle electronic systems.
Automotive Ethernet Cable
The automotive Ethernet cables show a wide range of application advantages in all aspects as an intelligent interconnection solution. It shows excellent flexibility in meeting different electromagnetic compatibility (EMC) requirement levels. Different automotive systems have unique requirements for EMC, and the Automotive Ethernet Harness can be customized to provide a flexible solution for specific requirements. Whether it is a high-end luxury model or a popular car, Automotive Ethernet cables can meet the requirements of all types of vehicles and provide a stable and reliable connection.
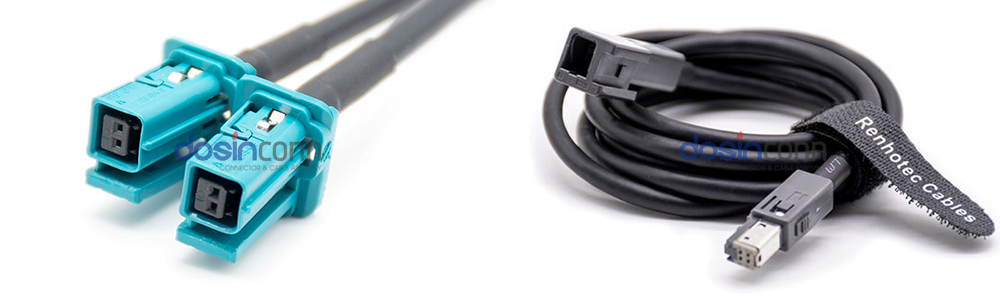
Automotive Ethernet cables are highly regarded in the industry for their superior cost effectiveness. Cost control has always been an important consideration in the automotive manufacturing process. Using an automotive Ethernet cable can optimize production costs while ensuring that quality and performance are not compromised. Compared to traditional connectivity solutions, the design of automotive Ethernet cable is more refined and the production process is more efficient, resulting in lower manufacturing costs and higher production efficiency. This enables automobile manufacturers to offer affordable vehicles while ensuring customer satisfaction with quality and performance.
The ease of installation of automotive Ethernet cables makes them invaluable in automotive manufacturing and repair. Time and efficiency are critical factors in the automotive manufacturing process. The designers of automotive Ethernet cables aim to make the installation process easier, thus reducing the workload of the manufacturer. In addition, for service personnel, ease of installation means faster repair times and lower repair costs. They are able to quickly diagnose and replace faulty harnesses to ensure proper vehicle operation. This provides convenience for vehicle owners while reducing the time and expenses required for repairs.