The continuous development of the automotive industry and the rising sales of cars have also provided a favourable opportunity for the development of new energy vehicles. New energy vehicles guided by the market environment are also an inevitable part of economic development. With the increasing number of automobiles, related industries have experienced significant growth. Among them, the automotive components industry has rapidly developed and become a crucial challenge in the automotive sector. Automotive wire harnesses, as fundamental components of automobiles, consist of various connectors. During the assembly process, it is essential to accurately assess the quality of wire harnesses as they directly impact the vehicle’s overall quality and performance.
In this regard, it is necessary to prioritize addressing potential errors that may arise in design and manufacturing, addressing the issues at their root. When dealing with automotive connectors, careful attention must be given to the placement of error prevention measures. Utilizing error prevention designs helps mitigate unnecessary risks, minimize product defects, and enhance the product quality and market competitiveness of automotive components. The application of error prevention techniques in connector selection plays a crucial role in many aspects.
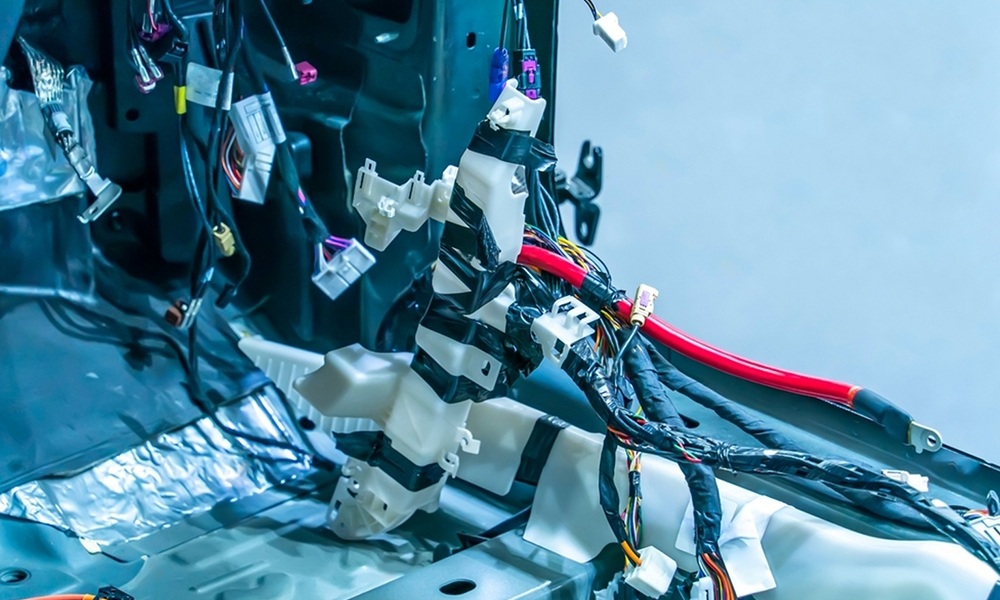
Error-Proof Technology for Automotive Connectors
Generally speaking, the main significance of error-proofing technology lies in the fact that it can give users better product experience and not provide customers with defective products; it also helps to improve the quality of the product itself and can reduce the number of rejects; it can also effectively reduce the cost of the manufacturing process and reduce the waste that may occur in manufacturing production. In general, there are several types of error prevention methods for connectors. They can be classified as follows: color-based error prevention, structural error prevention, dimension-based error prevention, component-based error prevention, and docking error prevention. They can effectively reduce the potential risk of product misalignment, omission and mixing. This approach is conducive to the better development of new energy vehicles in the market.
Specific Measures for Connector Error-Proofing
Error-Proofing in Structure
When designing wiring harnesses, it is common to find identical connectors in close proximity to each other. This can be accomplished by proactively selecting mutually compatible automotive connectors based on electrical ends, thus completing the error-proofing. Furthermore, this type of error-proofing has a very positive effect on the entire product development process, highlighting the primary role of the structure and ensuring that the project takes shape. In order to achieve this, it is necessary to refer to different electrical ends and select different connectors at an early stage of the design process in order to minimise the restrictions on the type of connector connection end and grinding tool.
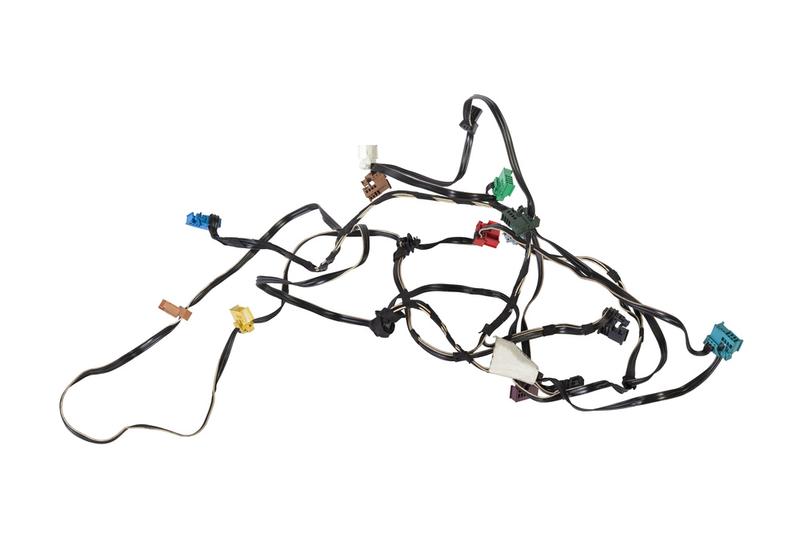
Error-Proofing on Components
During the connection of the wire harness, you can freely select the type of connector. Generally, there are several options: first, the selection is based on meeting the electrical end requirements, with emphasis on the automotive connector’s appearance. At the same time, the mating components should remain unchanged, but the shape and length can be reasonably modified to achieve misconnection prevention by altering appearance. Second, different connectors should be given different levels of importance during the manufacturing process. The connector itself does not change in design, but there is freedom to choose the back cover and lock of the connector. One can effectively ensure the manufacturing quality of the product by setting up error-proof points in the guide slots.
Error-Proofing in Colour
There is a more obvious method of error-proofing that is the color error-proofing method, which can more visually reflect the problems in the connection process. Colour proofing is a way of making things clearer at a glance, and its greatest advantage is its clarity. During the design process, it is often necessary to consider the limitations of automotive connectors components comprehensively. However, this alone may not achieve the goal of error prevention. Therefore, it is important to give due importance to color-based error prevention. By selecting connectors of different colors, one can achieve the goal of error prevention, thereby establishing a stronger foundation for the operation of the connectors.
Error-proofing in terms of dimensions
Dimension-based error prevention is particularly suitable for locations prone to errors. Generally, when the functions of various automotive connectors are relatively similar, it is necessary to determine the orientation of the fixed components by utilizing different dimensions. This approach ultimately achieves the goal of dimension-based error prevention. In the manufacturing process, the most scientifically sound dimension-based error prevention lies in prioritizing the connectors’ terminals. They should facilitate proper insertion while ensuring their uniqueness and accuracy. For example, when applying dimension-based error prevention to connectors A and B, it is crucial to consider that even though there may not be significant inherent differences between the two connectors, the dimension-based error prevention approach allows for proper insertion of connector A into terminal A and connector B into terminal B. This guarantees better uniqueness and accuracy in the connections between the connectors.
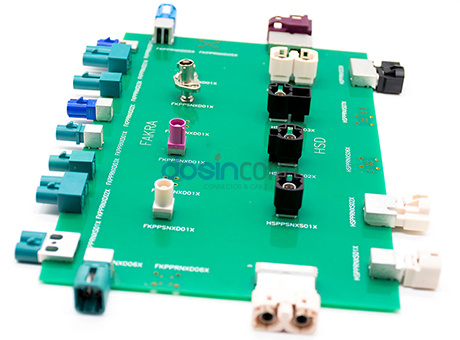
Error-proofing in the docking
There is also a relatively easy to appear a situation is the connector docking on the problem, for this case, it is generally not possible to color or shape error-proof. In this situation, it is necessary to actively dock the automotive connectors using specific measures to effectively prevent issues such as leakage and incorrect insertion, thereby establishing a stronger foundation for the connector docking process. For docking error-proofing, the main thing is to swap the male and female connectors at the docking end, using this method to allow the design of the entire error-proofing function to play..
To sum up, in the process of new energy vehicle design, we should pay attention to its scientific and rational nature, we should pay attention to the error-proof way of auto connector design connection, specific analysis and application of various error-proof ways, the problems of auto connector connection in a reasonable solution, so as to better achieve the level of automotive wiring harness, a greater realization of the scientific nature of automotive production, improve the quality and efficiency of products.